Enriching MEMS Sensor Use Cases In CE And IoT
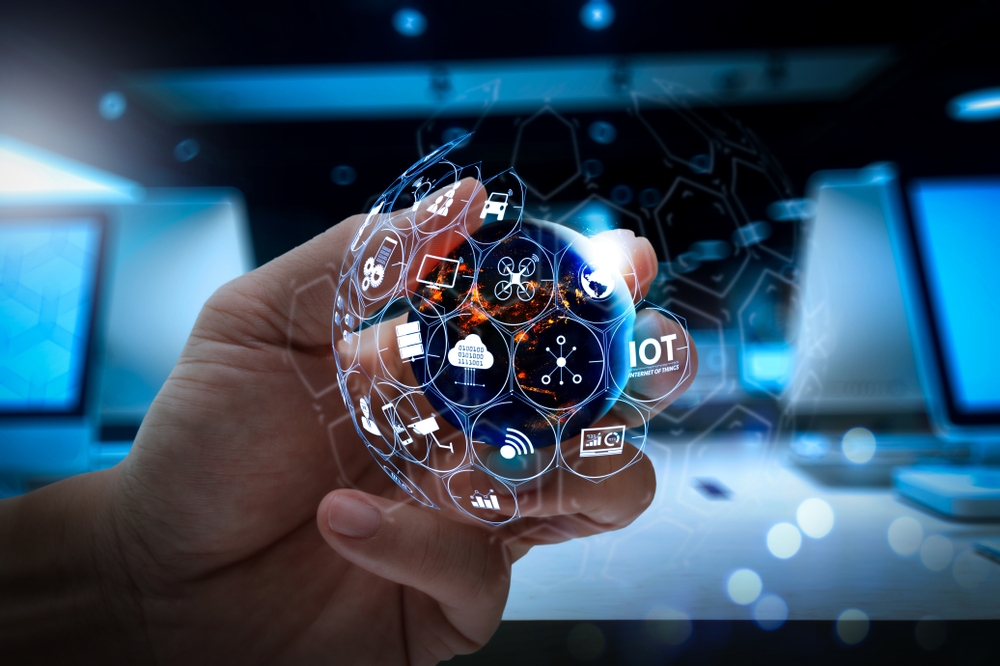
MEMS sensors are all around us. Today, there is at least one MEMS sensor in almost all state-of-the-art mobile consumer electronics (CE) devices. From smartphones over tablets and notebooks to smartwatches and hearables, MEMS sensors have taken over important key functions in these devices. They measure movement, acceleration, air pressure and quality, and much more. MEMS sensors themselves are undergoing continuous development processes to increase performance, reduce power consumption and shrink their physical size.
In parallel, more and more new sensor use cases are being developed with and around MEMS sensors. This is achieved either by intelligently combining them with other measurement technologies or by applying leading-edge technologies such as artificial intelligence (AI) and machine learning (ML).
In this article, we’ll discuss some of the latest solution examples at different complexity levels, explaining how new technological developments enrich sensor-related use cases for CE and Internet of Things (IoT) devices.
By Wolfgang Schmitt-Hahn, Bosch Sensortec
In the world of high-tech mobile CE devices, like smartphones, wearables, and hearables, it's a must to improve performance and reduce power consumption and size. Innovation is not limited to sensor hardware - software and algorithms are becoming increasingly important, too.
But what is the purpose of all this innovation? Primarily, it is to deliver better technical performance, which is critical for the designers of the corresponding CE device. For example, reducing the power consumption of the sensor leaves more battery capacity for other components or simply helps to extend the battery lifetime of the device. Similarly, a smaller sensor size helps to reduce the overall size of the CE device and makes it more comfortable to be used by the consumer.
Here we want to show you three examples of how innovation of MEMS sensor technology has enabled completely new use cases.
Dead reckoning extends battery life
The first example of a new use case is from the field of inertial MEMS sensors, which include accelerometers and gyroscopes. In combination with a geomagnetic sensor, they are typically used to determine the motion and orientation of a mobile device in three-dimensional space.
Now, combined with a sophisticated software algorithm, these sensors can be used to enable pedestrian dead reckoning (PDR), which basically means that you can track the movements of a person as they walk around carrying their smartphone. While there are some technical limitations with regard to the amount of time this can be done, recent advances in sensor precision and in the level of refinement of the software algorithms involved have improved this technology significantly.
Where may that be of use, considering that we usually have GPS available? Well, there are two use cases where it can be very helpful. Firstly, it can be valuable when GPS is either obstructed, which could be in ‘urban canyons' (between tall buildings) and forests, or not available at all, such as inside buildings.
Secondly, MEMS sensor-based PDR is much less power-hungry than GPS. For a smartwatch or true wireless stereo (TWS) earbuds, battery capacity is always a critical topic. So, by using both systems (GPS and PDR), the device can switch off GPS intermittently and then use the motion data from the inertial sensors, which operate at a much lower power consumption level. In fact, as shown in Figure x, this operation mode helps to significantly reduce the overall power consumption of this specific use case.
Figure 1: Block diagram of a system that can use GPS/GNSS and PDR data from inertial MEMS sensors.
Figure 2: Current consumption for the GPS/GNSS system, the PDR solution and the combined operation mode.
PDR+GPS (400m run)
Figure 3: The difference in accuracy when using duty-cycled GPS/GNSS, compared with the combination of GPS/GNSS and inertial MEMS sensor-based PDR.
Sniffing out wildfires
The second example involves a new use case for the identification of different smells, and to check ambient air quality. One of the main ways to do this is using state-of-the-art metal oxide- (MOX-) based gas sensors, which detect volatile organic compounds (VOCs).
That's two new pieces of jargon; what do they mean? Firstly, VOCs are organic chemicals that boil at low temperatures, so, if they are present, they are likely to be in the air around us as gas molecules. Typical VOCs include the perfumes and scents we can smell, as well as solvents and other pollutants.
Then, a MOX-based VOC gas sensor is based on measuring the electrical resistivity of the surface of micro-hotplates in the sensor, while they are being heated. These hotplates are coated in a layer of metal oxide. Varying the temperature during a measurement cycle leads to specific resistivity patterns, each of which is characteristic of a particular gas or gas mixture - for example, VOCs use up oxygen at the MOX surface, thus reducing the resistance.
The resulting patterns can then be analyzed using artificial intelligence (AI) in the form of machine learning algorithms. As a result - thus creating a new use case - it is possible to train the sensor and the related AI-software solution to identify certain “smells” from each other. In the home or workplace, this can be used to monitor air quality and alert residents of any unacceptable levels of gas present.
A very important application for this product solution, which is already in use, is wildfire detection. With connected sensors deployed over an area in a forest, gases and gas mixtures that are characteristic of wildfires can be detected and identified already in the formation phase of a wildfire, thus enabling emergency services to be alerted so that they can quickly extinguish the source of a fire. At the same time, this solution allows continuous refinement of the ML algorithm with regard to the sensitivity for the relevant gas mixtures: the sensors' software can be adjusted in the forest, to improve their accuracy.
Figure 4: Early detection of wildfires using a connected, ML-enabled VOC gas sensor network deployed in a forest.
Precise altitude measurement
The third example of how innovative sensor technologies enable new use cases is related to barometric pressure - also known as atmospheric pressure, which is the air pressure at any point. Barometric MEMS pressure sensors are used for making weather forecasts and monitoring altitude changes.
Their ability to determine altitude is based upon the so-called “barometric formula” that mathematically describes the relationship between changes in altitude and barometric pressure. Everybody knows the phenomenon of decreasing barometric pressure when climbing up a mountain, which usually requires ear clearing.
Barometric pressure sensors have become so precise in their measurements of air pressure that they can distinguish altitude changes in the range of 17 cm, about 6.7 inches. This is an incredibly accurate measurement - the 17 cm altitude difference is in the range of the height of a single step of a staircase, and measuring this altitude change is equivalent to measuring the deflection of the sensor's membrane when a mosquito sits down on it.
Such a sensor is thus capable of monitoring every single step when going up or down a staircase (Figure 5). Being able to determine whether a person is walking up or down stairs can be useful for indoor navigation applications, for example, and for activity trackers.
Figure 5: Latest development in barometric MEMS pressure sensors allows for the altitude change measurement of a single step of a staircase.
At the same time, these barometric MEMS pressure sensors have been shrunk to a footprint of only 2 x 2 mm2, with ultra-low power consumption in the range of just a few µA. This makes them ideally suited for use in true wireless stereo (TWS) earbuds.
Now, the new use case is a result of integrating a barometric MEMS pressure sensor into the earplug of a TWS. The wearer can just start doing their pull-up or push-up exercises and let the TWS count the repetitions. The altitude change during the exercise is being accurately monitored by the barometric MEMS pressure sensors. This has not been possible before - the increase in accuracy of the sensor has thus enabled a completely new use case.
Figure 6: Highly resolved measurement of altitude changes during fitness training using the latest, topnotch barometric pressure sensor integrated within the earbud of a TWS.
What can we learn from these three examples?
The evolution of new use cases for MEMS sensor solutions is driven by further development and refinement of software algorithms, making ever more sense of all the raw data already available. Applying AI/ML to intelligently decide and act based upon aggregated data at the edge opens up a completely new space for new uses never considered before.
At the same time, MEMS sensor hardware continues to improve, with smaller components, lower power consumption that improves battery life, and improved accuracy. All of this is provided in robust, reliable packages.
Finally, the hard work of continuously innovating sensor hardware and driving sensor technology forward pays off - with incredibly precise measurements paving the way to new use cases for MEMS sensors.