Smart Sensors Keep The Pressure Off
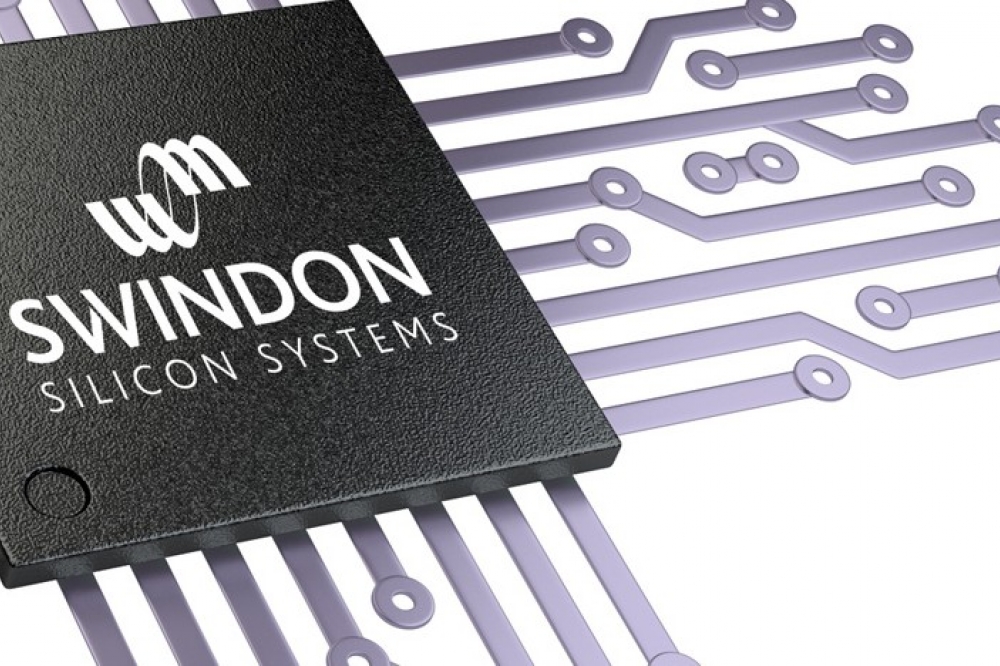
Real-time sensor data is enabling smart factories to better understand their own processes, allowing more efficient operations. One of the most diverse and widely deployed type of sensor in the industrial internet of things (IIoT) is the pressure sensor. Here, Richard Mount, Director of Sales at ASIC design and supply company Swindon Silicon Systems, explores how integrating ASIC technology with a MEMS pressure sensor keeps smart factories operating safely and efficiently.
Smart factories use connected devices, machinery and production systems to continuously collect and share data. This data is used to inform decisions, improve processes and address any issues that arise — ultimately improving manufacturing efficiency.
According to the 2021 State of Manufacturing Report from Fictiv, 95 per cent of manufacturers agree that digital transformation is essential to their company's future success. To collect the data necessary to enable digital transformation, smart factories use sensors to monitor a range of variables, such as the temperature of machinery, energy consumption, humidity and operating time. One such example of this is a pressure sensor.
Going with the flow
Differential pressure sensors measure the difference in pressure at two points and provide a comparative measurement between the two. They are frequently applied in industry to monitor processes where the medium is compared at two different points, for example the input and output of a filter.
If under normal conditions, the pressure between the influent pressure and the effluent pressure should be kept to a minimum, then by measuring the differential between the two, the data can show either a good operating condition or the onset of a failure. A failure such as a filter becoming blocked with contaminants would be detected due to the effluent pressure dropping, which would result in an increase in pressure difference.
If the pressure differential is detected, then this data can be used to alert factory employees of the issue so it can be rectified in a timely fashion. Where low power, size and performance is important, microelectromechanical systems (MEMS) technology is now widely used for pressure sensors, which provide high-pressure resolution in ultra-compact and thin packages.
HVAC systems
In industry, HVAC systems are vital to maintain air quality, employee health and quality assurance benchmarks. Accurate pressure measurement is essential for optimal HVAC system performance. Sensors play a major role in improving the efficiency of these systems by monitoring various parts of the system and confirming that all parts are functioning properly.
MEMS pressure sensors can measure air flow and pressure throughout the system for effective air distribution, optimising a factory's heating and cooling, as well as reducing energy consumption. The MEMS sensor measures pressure, be it absolute or differential, to provide real time analysis of the physical environment. This data is used to determine conditions and to make decisions accordingly, for example by alerting the system when maintenance and filter replacement is required, helping to keep the machinery and factory running efficiently.
The benefits of custom design
To enable a smart sensor, the MEMS pressure sensor requires additional functionality so the data can be conditioned, processed and communicated to the user. This can be achieved with a mixed signal ASIC that comprises signal conditioning circuitry, microcontroller and programmable software along with wired or wireless communications. The ASIC delivers optimised performance that cannot be achieved with off the shelf components. The MEMS sensor can either be integrated into the ASIC or as a separate die that's co-packaged with the ASIC in a System in Chip (SiP) configuration. In the case of pressure sensing and measurement, each sensor and ASIC can then be calibrated across variable pressures and temperatures to provide high performance accuracy.
Because ASICs are designed specifically for their intended application, they will deliver an optimised performance to the manufacturer's specific requirements. An experienced ASIC partner will be able to understand the system and identify where ASIC design can unlock improvements, to optimise the entire signal path down to the finest detail.
Robust and reliable
Industrial pressure sensors tend to be located in challenging environments but are expected to perform accurately for many years. When designing an ASIC, the developers integrate as much of the circuitry as possible into a single package, thus reducing component count, which in turn increases robustness and reliability.
Standard IC components will inevitably go obsolete when either the component supplier develops a new part or if the sales volume or revenue drops below a certain level, meaning that supplying the part is seen as no longer financially viable. Even if the new part is an upgrade of an existing version, it will likely be incompatible with the system and design engineers will have to constantly redesign to accommodate the new component.
In contrast, ASICs are designed to ensure obsolescence should never become an issue. Fabless ASIC suppliers, such as Swindon, design their ASICs with product longevity as part of the development planning process and will provide assurances of lifetime support. If in the unlikely event of a process obsolescence, Swindon will work closely with the customer to develop a non-obsolescence plan if required.
This plan uses techniques such as storing wafers in on-site dry nitrogen cupboards, which in effect provides a die bank, where silicon is available for in excess of 30 years. ASIC technology, with the correct partner, ensures your pressure sensor can continue to be supplied for the lifetime of your product, without the need for costly system redesign and requalification.
Keeping your IP safe
Intellectual Property (IP) protection is a key ASIC strength, and a reliable ASIC supplier provides its customers with full ownership of the completed system design, to ensure their system IP is for their benefit and their benefit only. Choosing an ASIC partner that does not sell standard parts will also alleviate the risk of IP potentially being used at a future date in an in-house standard product.
Industrial pressure sensors are fundamental in monitoring processes for many applications, such as maintaining optimised HVAC performance, and ensuring a factory operates efficiently. Integrating an ASIC with the pressure sensor provides both commercial and technical advantages and ensures that it will continue to function and be available for many years.

The leading global integrated photonics conference and exhibition will once again bring together key players from across the value chain for two-days of strategic technical sessions, dynamic talks and unrivalled networking opportunities.
Join us face-to-face on 28th – 29th June 2022
- View the agenda.
- 3 for the price of 1. Register your place and gain complementary access to TWO FURTHER industry leading conferences: CS International and PIC International.
- Email info@sensorsinternational.net or call +44 (0)24 7671 8970 for more details.
*90% of exhibition space has gone - book your booth before it’s too late!