The all-seeing eyes of Industry 4.0
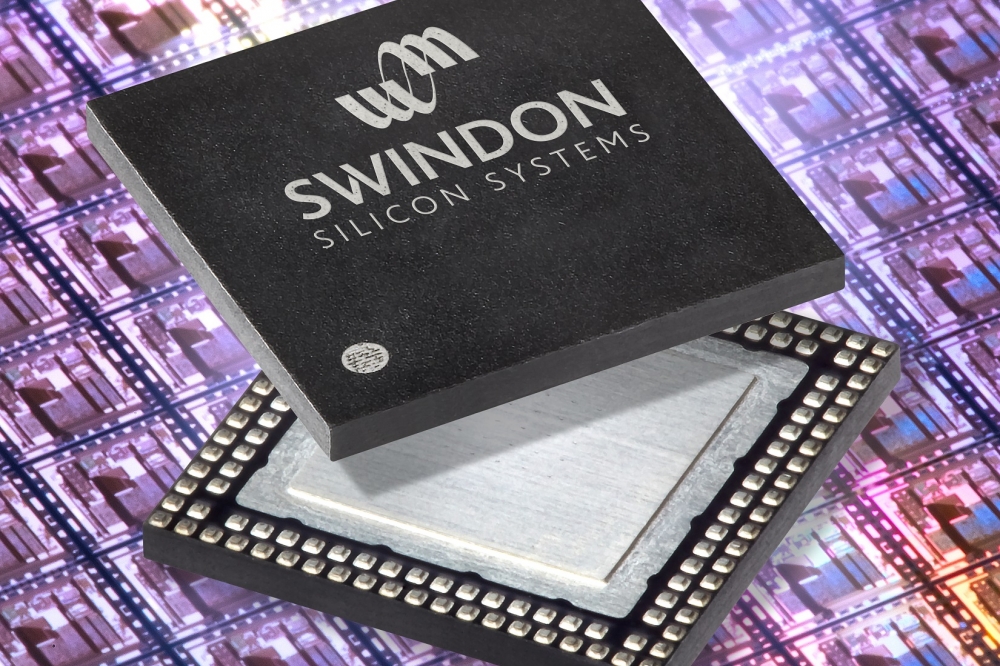
Industry 4.0 can be described as an eye-opening experience. The next phase in the digitalisation of the manufacturing sector, driven by the astonishing rise in data volumes, computational power and connectivity, allows manufacturers to see beyond the surface of their plant to uncover new ways of optimisation. One type of sensor that acts as a manufacturer’s eyes is the optical encoder. Here, Richard Mount Director of Sales at mixed signal ASIC specialist Swindon Silicon Systems, explores the technology and its supporting ASICs.
An optical encoder is a type of motion transducer that is commonly used to measure motion and provide feedback information in a closed-loop motion control system. This information can come in the form of several parameters, including direction, position and velocity of a moving part.
There are two types of optical encoder, reflective or transmissive. Optical encoders are typically made form a light source, a high-speed optical sensor, a readhead window and either an absolute or incremental scale to diffract or reflect the light source to provide positional data. The sensor may have additional elements to guide and shape the light such as lenses and beam splitting prisms. Its operation can be initiated by sending a demand to the readhead, instructing it to capture the position on the scale at that instant. The head responds by flashing a high-power LED source to illuminate the scale.
Crucially, its timing is controlled to preserve the relationship between demanded and reported position, one of the essential features for very high specification motion systems. Once the photons are captured by the photodetector, this signal is then digitised via an analogue-to-digital converter (ADC) and sent to a powerful digital signal processor (DSP) to obtain a relatively coarse position from the code embedded in the scale. After final error checking procedures, this positional information is then available to provide highly accurate position measurement to within one nanometre.
Optical encoders can be amazingly precise, making them a desirable choice for many applications where resolution matters. Potential applications could include, for example, providing precise and reliable motion feedback in robotics applications, in CNC machines to ensure machine tools operate at appropriate speeds, in automated dispensing of products and a myriad of other specialist uses.
Data decoding
So, how exactly can the data detected from the encoder turn into actionable insights? In an optical encoder, the sensing element is likely to be a phototransistor or photodiode. The photons from the incoming light are converted into an electrical signal, which can be conditioned and amplified. That signal is digitised with the output used for measurement data.
This processing unit will calculate the position from the encoder and can recognise events such as reference marks being passed, overspeed conditions and generating immediate interruptions towards the host system.
When an optical encoder is first developed, the constituent components may be commercial off-the-shelf (COTS) discrete components or integrated circuits (ICs). This can provide an adequate solution, particularly when production volumes are low. However, to truly ensure a product separates itself from the competition, it’s favourable to use ASIC technology.
ASIC technology brings many benefits. First, a reduced component count results in a smaller and more cost-effective product. Performance is enhanced with a higher speed and higher resolution encoder coupled with a lower lag. These benefits, used by a skilled ASIC design and supply company, will help a product stand out in the market.
For many customers, the protection of their Intellectual Property (IP) is extremely valuable, and ASICs provide this. Additional benefits, such as protection against obsolescence, smaller size, smaller power consumption and the knowledge that your product is unique further makes the ASIC route an attractive option for all optical encoder developers. An ASIC design partner, such as Swindon, will be able to assess a customer’s system and provide an optimised solution, designed specifically for their application requirements.
An optical encoder may not be the literal eyes of a manufacturer, but it certainly offers a layer of vision into their operations. While precise positioning can be supported through off-the-shelf circuitry, choosing an ASIC will undoubtedly afford many opportunities for an optimised and market leading product.